This is part two in Green Badger’s series of deep dives into the changes for LEED v4.1 and how they may affect project teams moving forward. For more resources, visit the other posts in our series below:
Part One: Introducing the LEED v4.1 Update
Part Two: Environmental Product Declarations, Option 1
Part Three: Sourcing of Raw Materials and Material Ingredient Reporting
Part Four: Low Emitting Materials
Part Five: Construction Waste Management
A couple of notes to start:
- The are all Green Badger’s opinions and interpretations.
- If you haven’t looked through the v4.1 beta guide from USGBC – download it now! That’s where the real meat and potatoes of the change details are actually listed.
- As always with USGBC, these may change at any time as 4.1 goes through the pilot.
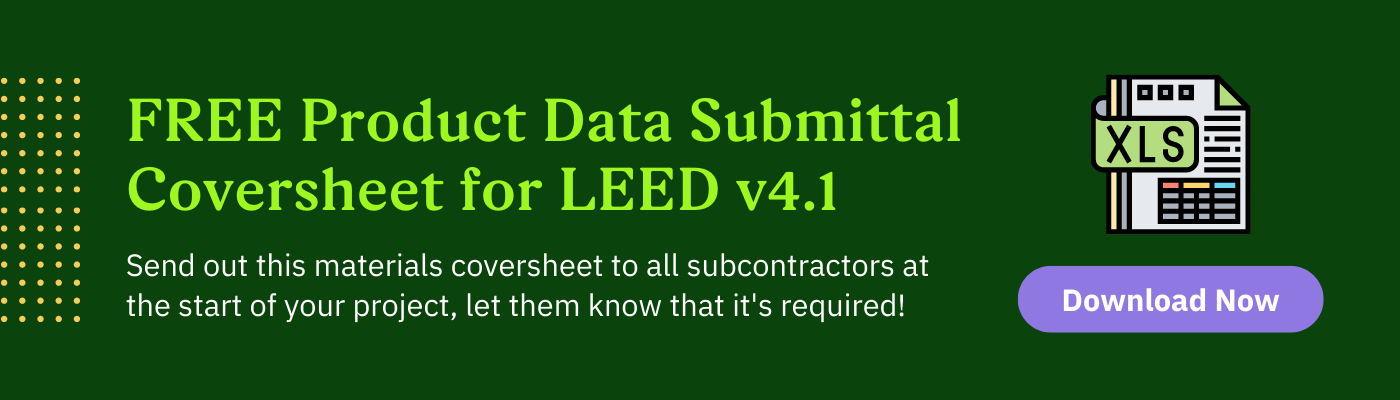
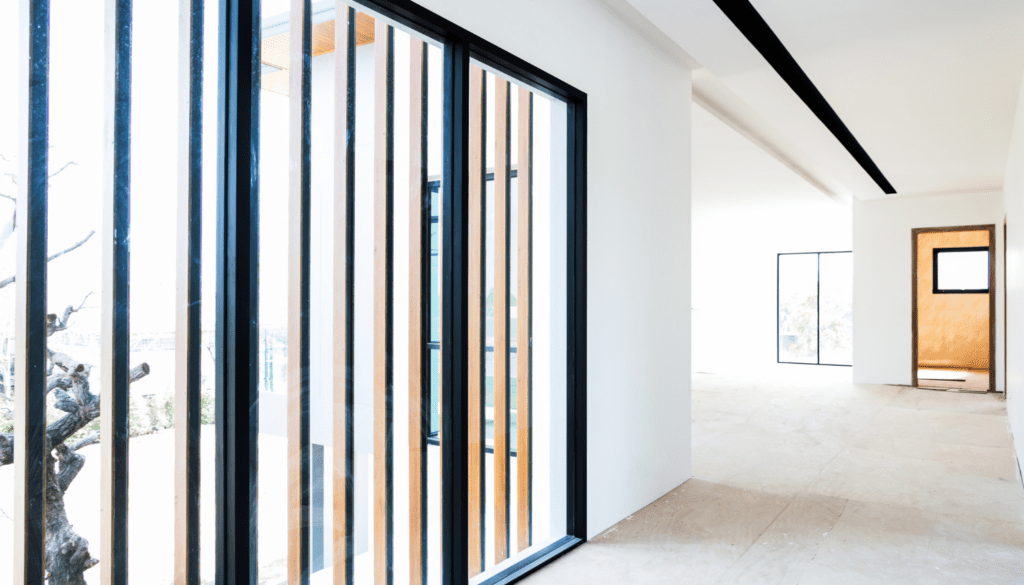
LEED v4.1 Environmental Product Declarations Option 1
On the surface, Option 1 for Environmental Product Declarations doesn’t look like it changes too much, which, since this credit was readily achievable for many projects in LEED v4, might be a good thing. In fact, it looks even easier at a casual read, especially easier for Core and Shell projects, which were challenged with limited interior fitout opportunities.
However, the devil is in the details.
Under v4, project teams needed 20 products with EPDs that weighed in according to the rigor and review the reports were subject to:
- Product specific – 0.25
- Industry wide – 0.5
- Product specific Type III, internally reviewed – 0.75
- Product specific type III, externally reviewed – 1.0
There are nuances and ISO standards for each type that the Badger won’t bore you with, but far and away, Product-Specific Type III was most commonly seen, followed by Industry-Wide for materials such as concrete, steel, wood, and gypsum board. As plenty of other articles from Green Badger demonstrate, those products, while not widely available for all types of products, were certainly available for enough commonly used construction materials that this credit option was achievable. Standard EPDs from UL, NSF, and ASTM all meet the requirements and provided straightforward enough documentation.
For v4.1, the requirement is still to use 20 different products for most BD&C projects. If you’re on a Core and Shell, Warehouse, or ID&C project, this drops to 10. Easy enough. Here’s where the broader differences come in – the weightings and the new requirements for the actual documentation.
- Product lifecycle assessment – 1.0
- Industry wide, company specific – 1.0
- Product specific Type III, internally reviewed – 1.0
- Product specific type III, externally reviewed – 1.5
Again, seems easy enough, but here’s where you need to dive into the v4.1 beta guide. Here’s a rundown of the specifics:
Lifecycle Assessment and EPDs in LEED v4.1 Environmental Product Declarations, Option 1
Lifecycle assessment and environmental product declarations need to have an LCA conforming to ISO 14044 (common for full EPDs). To be compliant, each one must have a LEED-specific summary sheet that shows the LEED requirements, the name/credentials of the person conducting the LCA, the type of software used, the date of assessment, and a link to the document. So – it’s not just enough to have the LCA/product declaration – it must have a LEED summary page per the guide to count.
Industry-Wide EPDs
Industry-wide EPDs now count for a full product! Sounds great! BUT – for industry-wide EPDs to count now, they must include the manufacturers as a specific participant. This means industry-wide EPDs done by associations no longer count because they don’t show every single manufacturer as a participant. So it looks like the EPD for concrete, steel, wood, type x gypsum and others (at least that we’ve seen in the past) may no longer count at all. Industry-wide EPDs must also provide a LEED summary sheet detailing the LEED requirements, the name/credentials of the person conducting the LCA, the type of software used, the date of assessment, reference to the PCR, regions covered under the EPD, and a link to the document. So – you need an EPD, it has to list the manufacturers, and it needs a separate summary sheet as well.
Product-Specific EPDs
Product Specific Internally/Externally reviewed EPDs now count as 1 (vs .75) and 1.5 (vs 1) respectively. These EPDs offer more credit, but additional caveats. These EPDs must be critically reviewed, which entails another ISO standard – ISO 14071. It doesn’t sound so bad until you go to ANY existing EPD which makes no reference to 14071. So is every existing EPD out of compliance for v4.1? We’ll have to wait and see how USGBC responds. Will every manufacturer have to pay to re-do their EPDs? Great business to be in if you are a certifier, not so good for the manufacturers if this is the case. Anecdotally, we’re hearing that USGBC recognizes 14071 won’t show up on EPDs for a while, so existing EPDs are safe. As long as the Externally Reviewed box is checked on the EPD, you should be able to count it as 1.5 products (which is great as that tends to be what almost all EPDs have anyway).
In the Badger’s opinion, if our anecdotal evidence is indeed true, this credit stays pretty much the same, and actually gets easier. The vast majority (if not all) Product-Specific Type III EPDs we typically see are externally verified, meaning they now count as 1.5 products, so instead of 20, you in effect only need 14. If you’re a C&S/Warehouse/ID&C project, you now only need 10 (which in effect is 7).
Most industry-wide EPDs published today are probably not much use going forward. Either way, it is likely a wash between 4.0 and 4.1 in our book, unless you’re a C&S/Warehouse/ID&C project, in which case you’re much better off with v4.1.
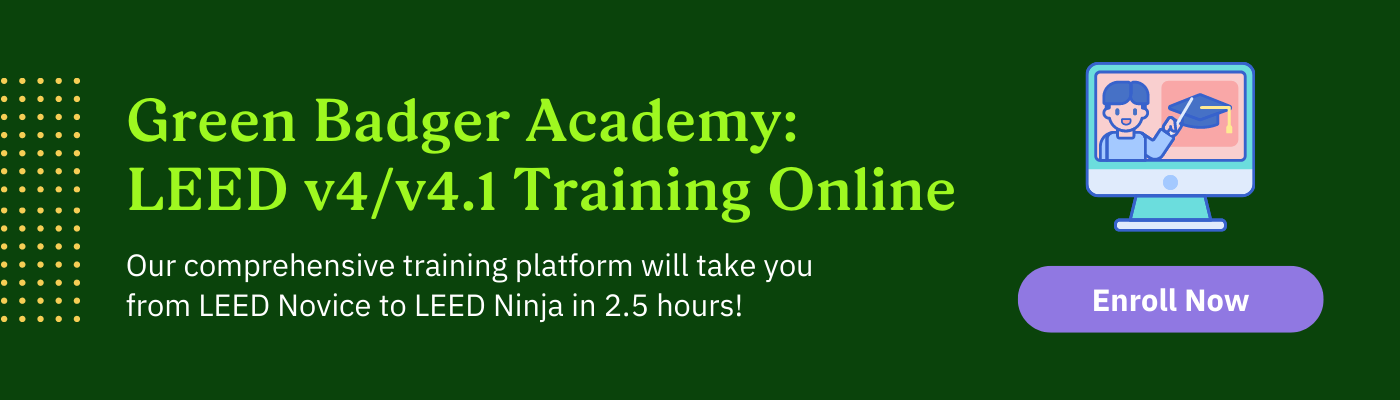