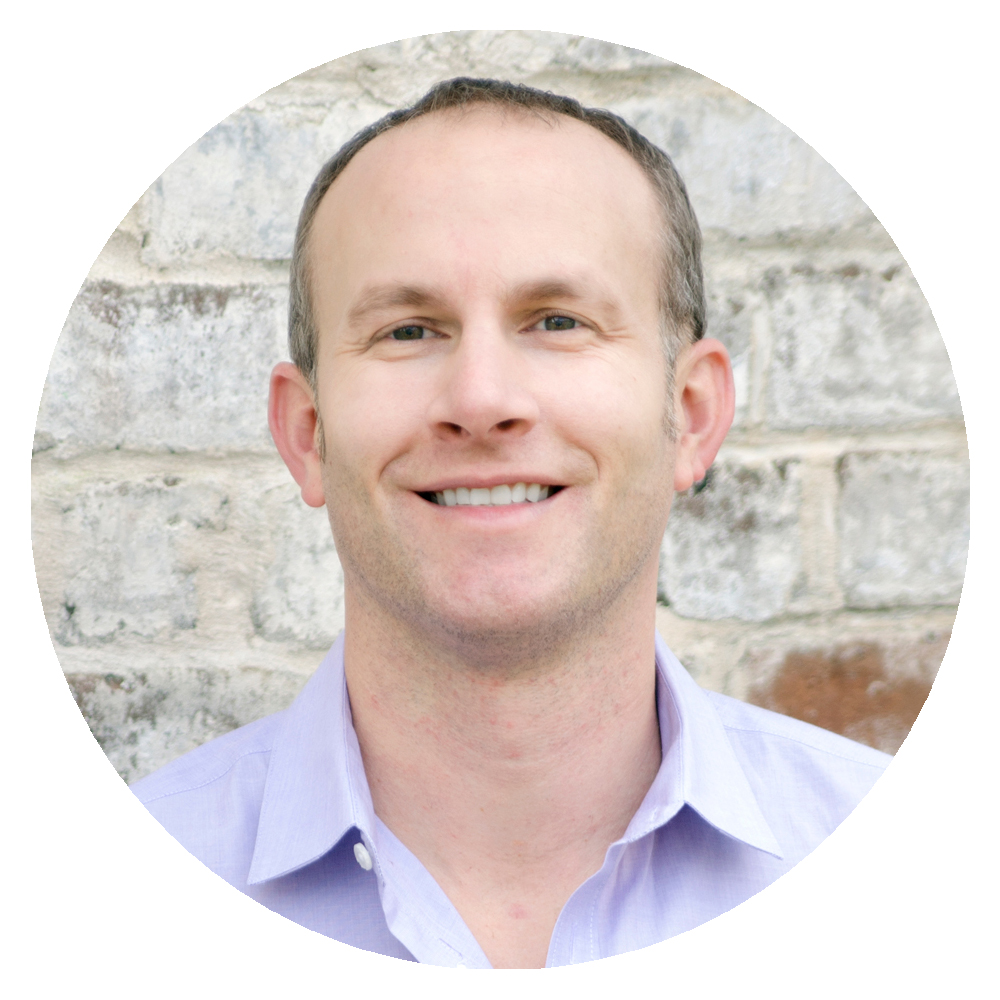
LEED v5 was balloted and approved by USGBC members in late spring, with the final rating system and initial reference guide being published in May 2025. Like all major LEED rating system updates, there are some substantial changes to drive the industry forward.
Decarbonization (from both materials and operations) is a huge focus in LEED v5, supported by efforts to electrify buildings, improve efficiency, and incorporate renewables (and MUST be incorporated to earn LEED Platinum). There’s a broader effort on planning and analysis, with new prerequisites required assessments on climate resilience, human impact, carbon and zero waste operations.
While there were significant updates to planning and building design, there were also some notable changes on the construction-related LEED credits. Here’s a summary of what’s new and notable, and what is relatively the same from prior versions.
New Prerequisite – Quantify and Assess Embodied Carbon
This is a completely new one! Project teams need to quantify the embodied carbon impacts (global warming potential or GWP) of the structure, enclosure, and hardscape materials for the project. At a minimum, include asphalt, concrete, masonry, structural steel, insulation, aluminum extrusions, structural wood and composites, cladding, and glass – all of which tend to have the biggest contributions to embodied carbon. Additionally, you need to identify the top three sources of embodied carbon on the project and describe how project-specific strategies were considered to reduce the impacts of these hot spots.
The prereq doesn’t require a reduction – it’s a baseline assessment of the embodied carbon of the primary materials in the project. This requires a material takeoff for each material so you can quantify using the global warming potential (GWP) from the product’s EPD. You can use broader tools such as EC3 or Green Badger’s new embodied carbon feature to quickly calculate the baseline embodied carbon. You’ll then need to identify what the top 3 contributors are, and whatever effort the team has incorporated to reduce the impact (i.e., concrete additives, low-carbon steel, etc)
New Credit – Reduced Embodied Carbon
This is a new credit that builds off the embodied carbon prerequisite. There are three options available depending on the approach teams want to take. Option 1 is very straightforward – 6 points are available for doing a whole building lifecycle assessment, with points awarded for 0-40% reductions in GWP.
WBLCA‘s assess all stages of a building’s life cycle in their calculation, including the product stage (Modules A1–A3), construction stage (Modules A4–A5), use stage (Modules B1– B7), end-of-life stage (Modules C1–C4) and the benefits and loads beyond the system boundary stage (Modules D). Comprehensive LCA software is required for this option.
Option 2 doesn’t require the comprehensive whole-building LCA, but requires EPD analysis for the project, with points awarded based on reducing the embodied carbon of the project based on EPD data for the project’s materials.
Option 3 is similar, but focuses just on the hardscape, structure, and enclosure materials that are required from the prerequisite. Baselines for these two options are the Carbon Leadership Forum Materials Baseline report, the US EPA, and similar standards.
Both options 2 and 3 require the actual product-specific EPDs where available (and industry-wide where not) and the exact quantity of each material, and will be compared to the standard baseline. Points are awarded for demonstrating reductions – for option 2, up to three points are available, and Option 3 offers 2 points for meeting the referenced standard for 3 or 5 of the structure/enclosure materials. Tools like EC3 or Green Badger’s new embodied carbon software can be used to demonstrate compliance.
New Prerequisite, Similar Concepts – Construction Management
Construction Management took the common LEED credit for Construction IAQ Management that has been around since the inception of LEED, and made it a prerequisite. No harm here, as every project pursued that credit anyway. What’s new is the inclusion of not just the typical SMACNA measures, but also Extreme Heat Protection, which is a smart addition to look out for the wellbeing of construction workers. At the end of the day, this will be a pretty straightforward prerequisite for construction teams and one that will seem very familiar for prior versions of LEED.
Updated – Building and Materials Reuse
This credit is a combination of the LEED v4 LCA credit for building reuse and pulling the material reuse efforts from the Sourcing of Raw Materials credits. Building reuse is straightforward – Points are awarded (up to 3) for reuse of existing building structure and enclosure elements for New Construction projects – you’ll need to quantify whether 20%, 35% or 50% of structure/enclosure were salvaged and reused in your project.
Material reuse is more complicated. Up to 2 points are available. Specific material types are identified – carpet, ceilings, furniture, and interior walls are the initial groups, but other materials for lumber, doors, casework, etc can be used. Teams need to quantify reusing 15% of one material (based onthe total amount used – i.e. if there is 1000 sf of carpet, 150 sf would need to be reused to earn one point. A second point is available for 30% reused, or reusing 15% of 2 target material types or 15% of 4 other material types.
Finally, up to 2 points are available for project teams that track emissions during construction activities – one point for fuel and utilities by the general contractor, and a second point is available for including subcontractors as well.
Updated – Building Product Selection and Procurement
This is a new credit, but is based on a lot of the familiar attributes from LEED v4.1 in the BPDO credits, and up to 5 points are available. Familiar terms like EPDs, HPD, Declare, and Cradle to Cradle all help products contribute to earning these credits. How they are earned is what is new. Rather than just total up the number of products that are compliant, it is now done by product category – and the entire product category must be compliant using a weighted average to count. The product categories are the same as the low-emitting categories, with the addition of plumbing fixtures.
All the aforementioned attributes can act as multipliers based on a super intuitive (cough, cough) table from USGBC that details whether an attribute is a Level 1, ,2 or 3. We’re going to skip all of that and make it easy – levels don’t matter – multipliers do.
We’ll be producing a comprehensive overview of this, but in short, if a paint has an EPD and HPD, it contributes to climate health and human health, so the multiplier is 2 – if you have $100 of that product, it counts as $200. Here’s a really basic example of the calculation:
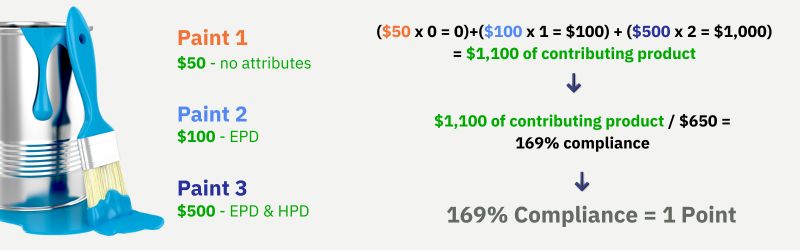
The more categories that exceed 100%, the better. Odds are project teams will pick up points for paint, flooring, ceilings and insulation pretty easily, so 3-4 points are pretty achievable here.
Similar – Low-Emitting Materials
Low Emitting Materials is pretty similar to LEED v4.1, with one major update – VOC content seems to no longer be required for adhesives and sealants and paints, and coatings. The only referenced requirement is the emissions evaluation, which is CDPH c1.2 – 2017 testing. So a bit more straightforward as there is only one attribute you need to track down.
The point total has been reduced. Two points are available (except for core and shell), but one is more likely to achieve 1 point. Projects must demonstrate 90% of paints/coatings, flooring, and ceilings are compliant, which is pretty achievable. A second point is available if you achieve option 1 AND are 80% compliant for two additional categories of Adhesives/sealants, walls, insulation, and composite wood OR 80% of the furniture category.
Similar – Construction and Demolition Waste Management
Construction Waste Management will seem pretty similar to other versions of LEED – you need to have a written CWM Plan, and you get 1 point for 50% diversion and 2 points for 75% diversion – no shocker on those requirements. The added requirements may be slightly more challenging. To earn 1 point, you also need to have at least 10% of the materials must be source-separated and sent to single-material recyclers – meaning you can’t count it if it is sorted at a commingled plant. Two points requires 25% source-separated. Realistically, most concrete is source-separated and weighs A LOT, so teams can likely earn this with commingled and source-separating concrete. About commingled – facilities must have a third-party verified facility recycling rate or you have to use the default rate of 35%, which will make earning even one point difficult.
The updates to LEED v5 for construction are mostly similar to past versions – outside of the new requirements around embodied carbon. For a deeper dive into the credit requirements and a more detailed analysis of how you can earn points and credits, join us for our LEED V5 for Construction webinar on July 30th.